How monocrystalline solar panels are made
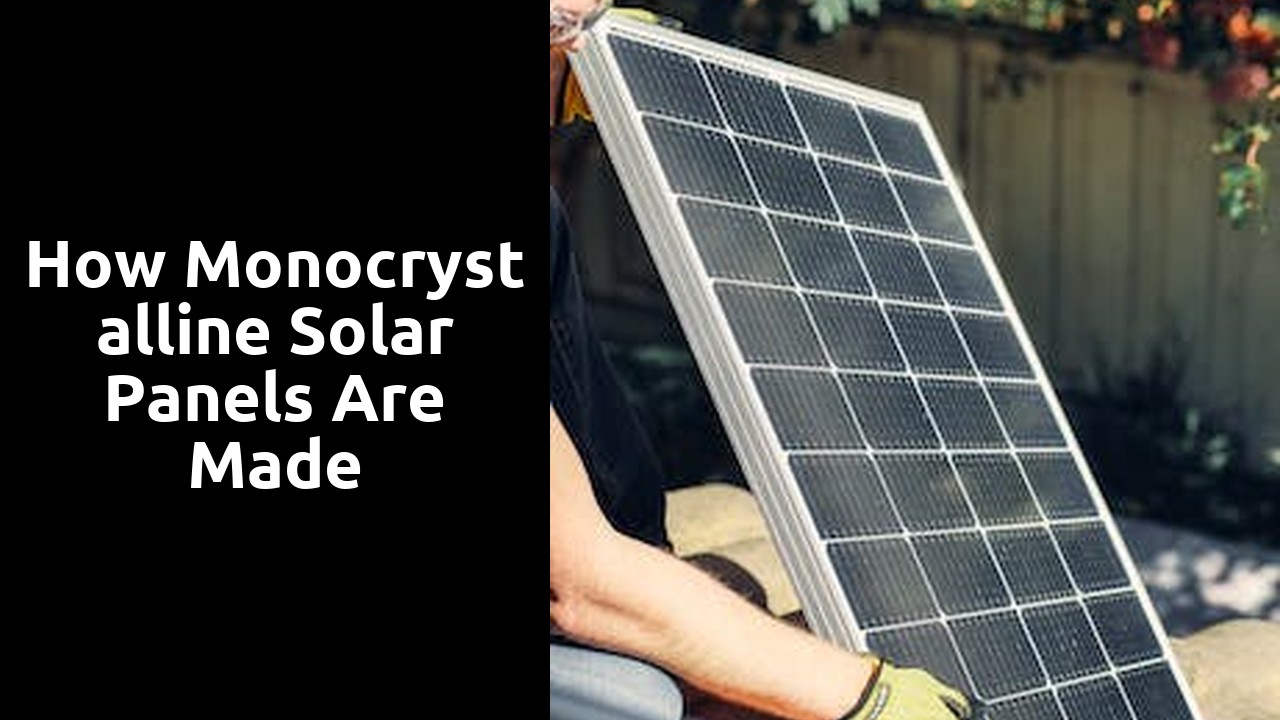
The Science Behind Monocrystalline Solar Panels: Exploring the Basics
Monocrystalline solar panels are a crucial component of the renewable energy landscape, harnessing the power of sunlight and converting it into electricity. These panels are made from a single crystal structure, typically composed of silicon, which allows for higher efficiency and performance compared to other solar panel technologies. The science behind monocrystalline solar panels lies in their ability to effectively capture and convert sunlight into usable energy.
One of the key features of monocrystalline solar panels is their high level of purity. This is achieved by sourcing high-quality silicon, the primary material used in panel production. Silicon is typically obtained through a process known as metallurgical grade refining, where impurities are removed to create a purer form of the element. This purified silicon is then further refined through the Czochralski method, in which a silicon seed crystal is submerged into a molten silicon melt and slowly drawn out to form a monocrystalline ingot. This ingot is then sliced into ultra-thin wafers, ready to be transformed into solar cells.
Sourcing High-Quality Silicon: The First Step in Panel Production
To ensure the production of high-quality monocrystalline solar panels, sourcing top-grade silicon is essential. Silicon, a chemical element derived from silicon dioxide, is the raw material used in the manufacturing process. Achieving a solar-grade level of purity, where impurities are minimized to less than one part per billion, is crucial for the effectiveness and efficiency of the panels.
The process begins with the careful selection of silicon suppliers. These suppliers undergo rigorous testing and evaluation to ensure that their materials meet the stringent requirements of the solar industry. High-quality silicon is not only important for the performance of the panels but also for their longevity. By sourcing silicon from reputable suppliers, solar panel manufacturers can ensure that they are starting with the best possible material, setting the stage for a successful production process.
From Silicon Ingots to Wafers: Understanding the Manufacturing Process
The manufacturing process of monocrystalline solar panels involves a series of intricate steps, starting from the production of silicon ingots to the final formation of wafers. Producing high-quality silicon ingots is the first crucial step in creating efficient photovoltaic cells. The purity of the silicon used directly affects the efficiency and performance of the solar panels. To achieve desired purity levels, raw silicon is melted and refined using various techniques such as the Siemens process or the Czochralski method.
Once the silicon ingots are formed, they are then sliced into extremely thin discs known as wafers. The thickness and quality of the wafers play a significant role in determining the overall efficiency of the solar panels. To achieve the desired thickness, the ingots are subjected to a process called ingot squaring – where unused portions are trimmed off – ensuring uniformity and optimal utilization of the ingots. These wafers undergo several rounds of chemical and mechanical polishing to further refine their surfaces, ensuring minimal defects and impurities. The final product, in the form of wafers, is then ready to move forward in the production process, bringing us one step closer to harnessing the power of solar energy.
Nurturing Perfection: The Art of Growing Monocrystalline Silicon
Monocrystalline silicon is the key ingredient in the production of high-efficiency solar panels. The process of growing monocrystalline silicon is a delicate art that requires expertise and precision. It all begins with the selection of high-quality silicon seeds, which are then placed in a crucible and melted down in a controlled environment.
Once the silicon has melted, it is carefully cooled down into a single crystal structure, which is known as a silicon ingot. This delicate process requires the perfect balance of temperature and pressure to ensure that the silicon grows in a uniform and flawless manner. Any impurities or inconsistencies can affect the performance and efficiency of the resulting solar panels.
To achieve the highest quality monocrystalline silicon, the growing process is continuously monitored, with experts performing regular inspections to ensure that the crystal structure remains intact. The temperature and pressure conditions are adjusted accordingly to maintain the perfect environment for growth. This meticulous attention to detail is what sets monocrystalline silicon apart from other types of silicon used in solar panel production, making it highly sought after for its efficiency and durability.
Slicing it Right: How Wafer Slicing Plays a Crucial Role
Wafer slicing is an essential step in the production of monocrystalline solar panels. During this process, silicon ingots are carefully cut into thin wafers, which are then used as the base material for the panels. The precision and accuracy with which the wafers are sliced play a crucial role in determining the overall efficiency and performance of the solar panels.
The wafer slicing process requires intricate machinery and expert operators who understand the delicate nature of the silicon material. The wafers need to be sliced with utmost precision, as even the smallest deviation in thickness can impact the panel's ability to convert sunlight into electricity. Additionally, the orientation of the slicing is also important, as it affects the electrical properties of the wafers. Therefore, manufacturers take great care to ensure that the slicing is done right, using advanced techniques and quality control measures to achieve the desired specifications. By slicing the wafers correctly, manufacturers can ensure that each panel they produce is of high quality and optimized for maximum energy conversion.
The Art of Surface Treatment: Preparing Wafers for Efficiency
Surface treatment is a crucial step in the manufacturing process of monocrystalline solar panels. It involves the preparation of wafers to maximize their efficiency in converting sunlight into electricity. The goal of surface treatment is to remove any impurities and defects on the wafer surface, creating a clean and smooth surface that allows for optimal light absorption.
One common method of surface treatment is called chemical etching. In this process, the wafers are submerged in a chemical solution that gradually removes a thin layer of the silicon material. This not only helps to eliminate any impurities, but it also creates a textured surface that enhances light trapping and absorption. By controlling the etching parameters such as time and temperature, manufacturers can achieve precise surface modifications to improve the wafers' performance.
Another important aspect of surface treatment is the application of anti-reflective coatings. These thin layers of material are applied to the front surface of the wafers to reduce the amount of light reflected back into the atmosphere. By minimizing reflection, more light can be absorbed by the solar cells, leading to higher energy conversion efficiency. Different types of anti-reflective coatings can be used, including silicon nitride, titanium dioxide, and various organic materials. The choice of coating depends on factors such as cost, durability, and performance requirements.
In conclusion, the art of surface treatment plays a vital role in preparing wafers for maximum efficiency in monocrystalline solar panels. By removing impurities, creating textured surfaces, and applying anti-reflective coatings, manufacturers can enhance the performance and optimize the energy conversion of the panels. Surface treatment techniques continue to be refined and improved, contributing to the ongoing advancement of solar panel technology.
Related Links
How monocrystalline solar panels are madeHow monocrystalline solar panels are made